3D Printing vs. Traditional Manufacturing: Which is Better?
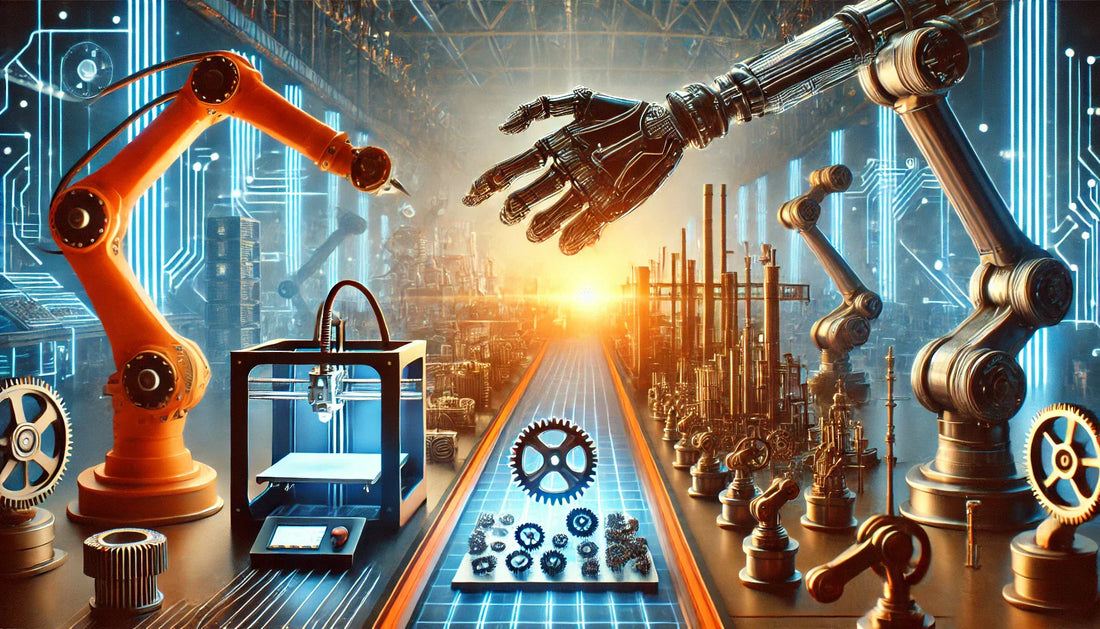
As technology advances, businesses and manufacturers are constantly evaluating whether 3D printing or traditional manufacturing is the better option. Both methods have their advantages and drawbacks depending on factors such as cost, efficiency, customization, and environmental impact. In this blog, we’ll explore a detailed comparison to help you determine the best choice for your needs.
1. Cost Comparison
3D Printing:
-
Lower initial investment since no molds or tooling are required.
-
Cost-effective for small-batch production and prototyping.
-
Higher material costs per unit compared to bulk manufacturing.
Traditional Manufacturing:
-
High setup costs due to tooling, molds, and large-scale machinery.
-
Economical for mass production, as unit costs decrease with volume.
-
Lower material costs due to bulk purchasing.
Verdict: 3D printing is ideal for prototyping and small runs, while traditional manufacturing is more cost-effective for mass production.
2. Efficiency and Speed
3D Printing:
-
Rapid prototyping and on-demand manufacturing.
-
Longer print times for complex designs.
-
No need for assembly in many cases, reducing production steps.
Traditional Manufacturing:
-
Faster production rates once molds and tools are ready.
-
Requires assembly lines and skilled labor, increasing production time for complex items.
-
Efficient for high-volume production but slow for small-batch customization.
Verdict: 3D printing wins for fast prototyping and customization, while traditional methods dominate in large-scale production.
3. Customization and Design Complexity
3D Printing:
-
Allows for intricate, highly detailed, and custom designs.
-
No additional costs for design changes.
-
Great for industries like medical implants, jewelry, and aerospace.
Traditional Manufacturing:
-
Customization requires expensive mold changes or retooling.
-
Limited complexity due to machining and mold constraints.
-
Best suited for uniform, standardized production.
Verdict: 3D printing is the clear winner for customization and intricate designs.
4. Environmental Impact
3D Printing:
-
Less material waste since only the required amount is used.
-
Some materials are recyclable, but options are limited.
-
Lower energy consumption for small-scale production.
Traditional Manufacturing:
-
Significant waste from excess materials, scrap, and defective parts.
-
Higher energy consumption due to mass production machinery.
-
More efficient for bulk production, reducing per-unit energy use.
Verdict: 3D printing is more sustainable for small-scale production, while traditional manufacturing is more efficient for mass production.
5. Applications and Industries
3D Printing is Ideal for:
-
Prototyping and product development.
-
Medical applications (custom prosthetics, implants, and dental products).
-
Aerospace and automotive industries for lightweight, complex parts.
-
Customized consumer goods like jewelry, phone cases, and home decor.
Traditional Manufacturing is Best for:
-
Mass production of consumer electronics, vehicles, and household items.
-
Textiles and packaging, where production speed is critical.
-
Heavy machinery and structural components requiring high durability.
Final Verdict: Which One Should You Choose?
The best choice depends on your needs:
-
Use 3D printing if you need customization, rapid prototyping, or small-batch production.
-
Use traditional manufacturing if you need mass production, cost efficiency for bulk orders, or long-term durability.
-
A hybrid approach (using 3D printing for prototypes and traditional methods for final production) can offer the best of both worlds.